The Essential Guide to Welding for Heavy-Duty Trucks: Types, Techniques & Benefits
Welding is vital for heavy-duty truck repair, restoring strength and durability. Learn about MIG, TIG, stick, and FCAW techniques to save costs, extend lifespan, and ensure safety. Proper methods and precautions can keep your fleet reliable and eco-friendly for years.
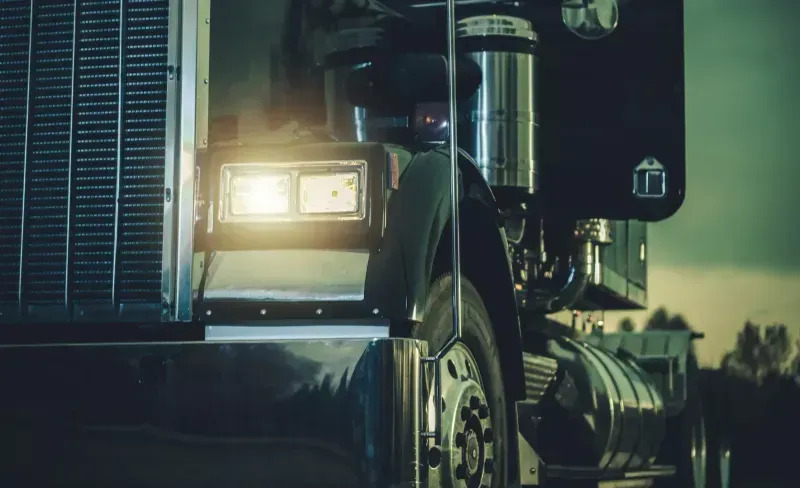
Welding is the backbone of heavy-duty truck repair and maintenance, playing a critical role in restoring structural integrity and enhancing durability. From mending a cracked chassis to fabricating custom parts, understanding the types of welding, mastering proper techniques, and appreciating the benefits can save time, reduce costs, and ensure safety.
This guide will demystify welding for heavy-duty trucks so you can make informed decisions about repair methods and materials.
Types of Welding for Heavy-Duty Trucks
Welding isn’t one-size-fits-all. Choosing the right method depends on the material, application, and the truck’s specific needs. Below are the most common types:
MIG Welding (Metal Inert Gas)
MIG welding, also known as Gas Metal Arc Welding (GMAW), is a common method for truck repairs. It’s highly versatile and works well on thicker metals like steel and aluminum.
- How it Works: A continuous wire electrode is fed through a welding gun, melted, and joined to the base material while shielded by an inert gas (usually argon or a mix).
- Best For: Frame repairs, exhaust systems, and body panels.
TIG Welding (Tungsten Inert Gas)
TIG welding, or Gas Tungsten Arc Welding (GTAW), is all about precision. While it requires more skill and time, the results are seamless and high-quality.
- How it Works: A tungsten electrode creates the arc, and a filler rod is used separately. Inert gas shields the weld area.
- Best For: Delicate parts like fuel tanks and intricate aluminum components.
Stick Welding (Shielded Metal Arc Welding)
Stick welding is a favorite for rugged tasks in challenging environments. It’s ideal for on-the-spot repairs when portability is key.
- How it Works: A flux-coated electrode melts to fuse metals, and the flux creates a protective layer against contaminants.
- Best For: Structural frame repairs and heavy steel components.
Flux-Cored Arc Welding (FCAW)
This technique excels outdoors, like MIG welding, but without a shielding gas.
- How it Works: A tubular wire filled with flux melts to create a weld, forming a slag that protects the molten pool.
- Best For: Repairs on truck beds and undercarriages.
Essential Welding Techniques
Welding is as much about technique as it is about tools. Master these practices to ensure a durable and safe weld:
1. Material Preparation
Before welding, clean the surface thoroughly to remove rust, paint, or oil. Use a grinder or wire brush for the best results. Preparation leads to strong welds.
2. Preheating
Certain metals, such as steel or cast iron, may require preheating to prevent cracking. This is especially true for welding thick truck frames.
3. Correct Positioning
How a weld is positioned—flat, horizontal, vertical, or overhead—affects penetration and strength. Flat welding, for example, often produces the strongest results.
4. Proper Heat Control
Overheating can cause warping or burn-through, especially on thinner materials. Use a lower amperage for precise control.
5. Post-Weld Inspection
After welding, inspect for defects like cracks, slag inclusions, or undercutting. Non-destructive testing (NDT) methods, like dye penetrant or ultrasonic testing, should be used if needed.
Benefits of Welding for Heavy-Duty Trucks
Welding offers a range of advantages, making it indispensable for maintaining and improving heavy-duty vehicles:
1. Cost-Effective Repairs
Why replace a part when you can weld it? For instance, a cracked exhaust manifold or damaged chassis can be restored without sourcing costly replacements.
2. Custom Fabrication
Welding allows for customization, from mounting brackets to load-bearing structures. This is especially useful for fleets with unique specifications.
3. Extended Lifespan
Reinforcing weak or damaged areas with welding extends a truck’s service life, preventing catastrophic failures down the road.
4. Enhanced Safety
Welded reinforcements ensure the structural integrity of critical components, reducing the likelihood of breakdowns during operation.
5. Environmental Benefits
Welding reduces waste by salvaging and restoring old parts rather than discarding them, aligning with eco-friendly practices.
Safety First: Welding Precautions
Heavy-duty truck welding has risks like burns, electric shocks, and exposure to toxic fumes. Follow these safety tips:
- Always wear a welding helmet with the appropriate shade.
- Use flame-resistant clothing and gloves.
- Ensure proper ventilation, especially when working with galvanized metals.
- Store gas cylinders upright and secure.
Conclusion
Welding is an art and science essential for the upkeep of heavy-duty trucks. Whether you're performing routine maintenance or custom fabrications, understanding the types of welding, employing the right techniques, and leveraging its benefits can make all the difference. Welding can keep your fleet in top condition for years with proper training and tools.